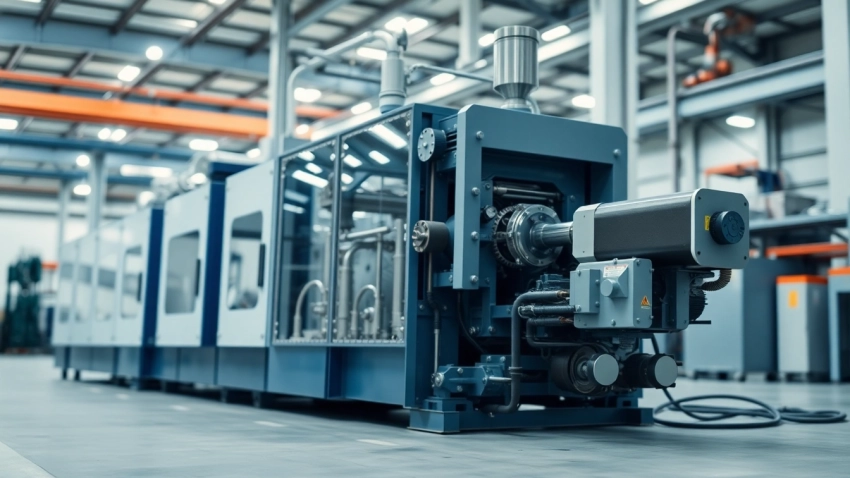
Leading Blow Molding Machine Manufacturer: Revolutionizing Production Efficiency
Understanding Blow Molding Technology
Blow molding is an essential manufacturing process used across various industries to produce hollow plastic objects. From bottles to containers, the significance of blow molding machines cannot be overstated in the modern manufacturing landscape. Selecting the right Blow Molding Machine Manufacturer can lead to improved efficiency and reduced production costs. In this comprehensive guide, we delve into the intricacies of blow molding technology and its applications.
What is Blow Molding?
Blow molding is a manufacturing process that involves inflating molten plastic material inside a mold to create a desired shape. This technique is primarily used to produce hollow plastic parts and is a critical process in the production of containers, bottles, and industrial parts. The method is favored for its efficiency and versatility, making it adept at meeting the diverse needs of various industries.
The Molding Process Explained
The blow molding process is generally divided into three main steps: extruding the parison, molding, and cooling:
- Extruding the Parison: The process begins with plastic pellets being melted and formed into a continuous tube called a parison.
- Molding: The parison is then clamped into a mold, and air is introduced to inflate it against the mold walls, taking the desired shape.
- Cooling: Finally, once the part has been formed, it is cooled and released from the mold.
This simple yet effective process allows manufacturers to produce high volumes of consistent parts quickly, enhancing productivity.
Types of Blow Molding Machines
Blow molding machines come in several types, each designed for specific uses:
- Extrusion Blow Molding (EBM): This type uses a continuous tube of molten plastic that is then inflated in the mold to create hollow parts. EBM is ideal for making large volumes of bottles and containers.
- Injection Blow Molding (IBM): A combination of injection and blow molding, this method involves creating a preform that is then inflated to shape. It is more precise and often used for smaller, more detailed components.
- Stretch Blow Molding (SBM): This is used primarily for PET bottles, where the plastic is stretched to enhance strength and clarity, providing thinner wall sections and superior finish.
Choosing the Right Blow Molding Machine
The choice of a blow molding machine significantly impacts production efficiency and product quality. Several factors should be considered when selecting the right equipment.
Factors to Consider for Optimal Performance
When selecting a blow molding machine, consider the following aspects:
- Production Volume: Assess the daily production volume to determine the machine size and type required.
- Material Compatibility: Be aware of the types of plastic materials you intend to use, as different machines have varying compatibility with materials like PET, HDPE, and PVC.
- Energy Efficiency: Choose machines that minimize energy consumption to save on operational costs.
- Space Requirements: Ensure the selected machine fits your facility’s footprint and operational workflow.
Customizable Features for Your Needs
Modern blow molding machines often come with customizable features that can enhance overall productivity:
- Automation: Automated systems can reduce labor costs and increase precision. Look for machines equipped with robotic arms for greater efficiency.
- Multi-layer Capabilities: Some machines allow for the production of multi-layer products, which can improve barrier properties and sustainability.
- Quick Changeover: Features that allow for quick adjustments and changeovers to produce different product lines without significant downtime are highly beneficial.
Comparative Analysis of Top Manufacturers
Several notable manufacturers lead the blow molding industry, each bringing unique technologies and innovations:
- Uniloy: A major player in blow molding technology, renowned for providing diverse blow molding solutions including molds and tooling.
- Wilmington Machinery: Recognized for its high-speed rotary extraction blow molding machines, ideal for large production runs.
- Jomar Corporation: Celebrated for their injection blow molding machines, especially suited for high-precision applications.
Industry Applications of Blow Molding Machines
The versatility of blow molding technology has led to its adoption across numerous sectors, significantly enhancing manufacturing processes.
Common Uses Across Different Sectors
Blow molding machines are integral to various industries:
- Food and Beverage: Commonly used for producing bottles and containers that require stringent hygiene standards.
- Consumer Goods: Produces parts for personal care items, cleaning supplies, and toys.
- Industrial Applications: Utilized in creating tanks and containers for chemical storage.
Case Studies: Success Stories from Our Clients
Exploring real-world applications gives insight into the impact of blow molding technology:
- Success with Recyclable Products: A client produced eco-friendly bottles using EBM technology, resulting in a 30% reduction in material waste.
- Streamlined Production: By switching to a fully automated blow molding line, a manufacturer quadrupled their output while lowering labor costs by 25%.
Future Trends in Blow Molding Applications
The future of blow molding looks promising with emerging trends:
- Sustainability: There’s a growing demand for recyclable materials in blow molded products, pushing manufacturers to innovate environmentally friendly solutions.
- Smart Manufacturing: The integration of Industry 4.0 principles will enhance real-time data analytics and machine learning capabilities in blow molding processes.
Cost Considerations in Blow Molding Machine Procurement
Investing in blow molding technology requires a thorough understanding of potential costs involved to ensure sound financial decisions.
Understanding Pricing Models
Pricing for blow molding machines can vary significantly based on several factors:
- Machine Type: Generally, IBM machines are priced higher than EBM due to their complexity.
- Features: Additional features such as automation, multi-layer capabilities, and customization options can increase the cost.
- Brand and Reputation: Established manufacturers often cost more due to their market reputation and warranty offerings.
Total Cost of Ownership Explained
The total cost of ownership (TCO) covers not only the purchase price but also:
- Installation and training costs
- Maintenance and repair expenses over time
- Energy consumption costs during operation
- Potential downtimes and lost productivity costs
Careful evaluation of TCO can lead to more informed purchasing decisions, ensuring long-term profitability.
Financing Options for Businesses
Financing options are often essential for businesses looking to invest in blow molding machines:
- Leasing: This option allows companies to use machines without the large upfront costs of purchasing.
- Bank Loans: Traditional loans from financial institutions can provide capital for purchasing machinery.
- Manufacturer Financing: Some manufacturers offer financing plans or partnerships to assist with the acquisition costs.
Maintenance and Support for Blow Molding Machines
Regular maintenance of blow molding machines is crucial for ensuring long-term performance and operational efficiency.
Routine Maintenance Tips for Longevity
Follow these maintenance tips to enhance the longevity and functionality of your machines:
- Regular Cleaning: Keeping machines clean from plastic residues helps in preventing jams and clogs.
- Scheduled Inspections: Routine inspections to check for wear and tear or any irregular operation can caught issues before they worsen.
- Lubrication: Regular lubrication of moving parts minimizes friction and wear over time.
Finding Reliable Technical Support
Technical support is essential, especially during machine malfunctions:
- Manufacturer Support: Most manufacturers offer technical support and service plans for troubleshooting.
- Third-party Services: Consider contracting reliable service technicians who specialize in blow molding machinery for additional support.
Training Resources for Your Team
Providing proper training for team members operating blow molding machines is critical:
- Manufacturer Training Programs: Many manufacturers provide training sessions on machine operation and maintenance.
- Online Resources: Utilize online tutorials, webinars, and other digital resources to enhance your team’s understanding.
Leave a Reply