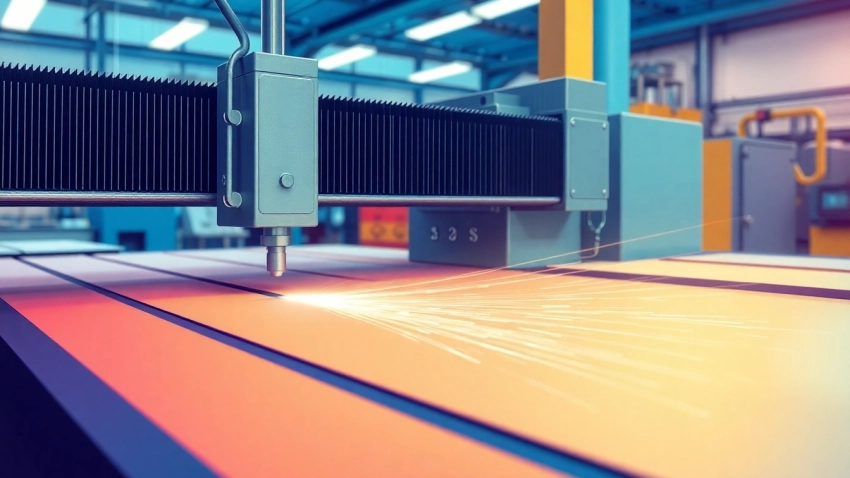
Enhancing Manufacturing Efficiency with Precision Die Cutting Solutions
Understanding Precision Die Cutting
What is Precision Die Cutting?
Precision die cutting is a manufacturing process that involves cutting materials into specific shapes and sizes with great accuracy. This technique is widely used across various industries to produce intricate parts and components that meet exacting quality standards. By utilizing specialized tools known as dies, manufacturers can efficiently produce large quantities of identical pieces while maintaining tight tolerances. The appeal of precision die cutting lies in its ability to process materials like paper, cardboard, plastic, rubber, and even metals, providing versatility and reliability in production. Precision die cutting techniques have revolutionized how products are manufactured, particularly in sectors such as automotive, electronics, and medical devices, where precision and efficiency are paramount.
Key Advantages of Precision Die Cutting
One of the core benefits of precision die cutting is the capabilities it offers in terms of speed and efficiency. Unlike traditional cutting methods, precision die cutting allows for high-volume production while ensuring uniformity across all parts produced. Additional advantages include:
- High Tolerance Levels: Parts can be created with exceptionally tight tolerances, often within +/-0.005 inches, making them suitable for applications that require precision engineering.
- Versatility: This method can be applied to various materials, including soft and hard substrates, opening pathways for diverse applications.
- Cost Efficiency: While initial die creation may carry a cost, the long-term value is profound given the reduced waste and enhanced production speeds.
- Complex Designs: With precision die cutting, intricate shapes can be achieved without compromising the structural integrity of the materials, allowing for creative and functional designs.
- Minimal Secondary Processes: Many precision die cutting processes also incorporate additional features such as embossing, scoring, and folding, reducing the need for multiple operations.
Common Applications of Precision Die Cutting
Precision die cutting finds widespread use across numerous sectors. Some common applications include:
- Automotive Components: Producing gaskets, insulation parts, and seals with high durability and reliability.
- Electronics: Creating custom foam inserts for packaging, as well as precision cut parts for electrical devices.
- Medical Devices: Manufacturing components such as surgical kits, packaging, and biomaterials with stringent health and safety compliance.
- Consumer Products: Developing packaging solutions and promotional materials with vibrant graphics and unique shapes that captivate customers.
- Textiles: Cutting fabrics and other soft materials for everything from fashion to industrial applications.
Types of Precision Die Cutting Techniques
Rotary Die Cutting Explained
Rotary die cutting utilizes a cylindrical die and a rotary press to produce parts continuously. The die is wrapped around a cylinder, and as the material passes through, it is cut into shape in a seamless, efficient manner. This technique is especially beneficial for large volume production runs, as it minimizes downtime and increases throughput. Rotary die cutting excels in scenarios where continuous feeding of material is essential, making it widely used in industries such as packaging and label production.
Flatbed Die Cutting Overview
Flatbed die cutting is a more traditional method where a flatbed press applies pressure to a stationary die over the material to be cut. This method is typically suited for smaller production runs or for materials that require a higher degree of thickness. Flatbed die cutting offers flexibility in designing and modifying dies, which can be advantageous when working with complex shapes or multiple designs across a single run.
When to Use Laser Cutting
Laser cutting has gained popularity as a precision die cutting method due to its ability to manage intricate designs and high detail. This method utilizes a focused laser beam to cut through materials, making it an excellent option for parts that demand extreme accuracy and complex patterns. Industries that commonly turn to laser cutting include bespoke crafting and short run manufacturing, particularly for prototypes or designs that may undergo frequent changes.
Choosing the Right Die Cutting Service
Factors to Consider for Precision Die Cutting
When selecting a die cutting service, several factors should be taken into account to ensure that the partnership aligns with your manufacturing needs:
- Material Compatibility: The service should be experienced in working with the specific materials relevant to your project.
- Technology Capabilities: Ensure that the provider utilizes modern equipment and techniques that can cater to both high volume and specialized production needs.
- Experience and Expertise: A provider with a solid track record in the industry can offer insights that may help refine your designs and improve efficiency.
- Quality Assurance Practices: A commitment to quality standards should be evident, as this will impact the outcome of the parts being produced.
- Customer Support: Responsive customer service is essential for addressing any questions, concerns, or adjustments needed throughout the production process.
Evaluating Service Providers
To evaluate potential precision die cutting service providers effectively, consider the following steps:
- Research and compile a list of potential vendors based on industry reputation and reviews.
- Request samples of previous work to evaluate quality and precision.
- Ask about their experience in your specific industry to assess if their capabilities align with your requirements.
- Discuss lead times and production schedules to ensure your timeline aligns with their capabilities.
- Review their pricing structure and ensure that it’s transparent, with no hidden costs.
Cost Considerations for Precision Die Cutting
The cost of precision die cutting can vary significantly based on a variety of factors:
- Type of Die: Custom dies may have higher upfront costs, but they enable large production runs that can offset initial investment.
- Material Type: Different materials may come with varying costs; harder materials often require more robust dies and equipment.
- Volume of Production: Typically, as the volume increases, the per-unit cost decreases due to efficiencies gained.
- Complexity of Design: More intricate designs may require more elaborate dies and setup processes, impacting overall costs.
Maintaining Quality in Die Cutting
Common Challenges in Precision Die Cutting
Although precision die cutting offers many advantages, various challenges may arise during the process:
- Material Distortion: Some materials may not retain their shape after cutting, particularly if they have not been adequately prepped or handled.
- Inconsistent Quality: Variability between batches can occur if there are fluctuations in material quality or machine calibration.
- Equipment Wear: Regular maintenance and upgrade cycles are crucial to avoid defects arising from worn cutting dies.
- Design Adjustments: Making changes to designs too late in the process can lead to increased costs and delays.
Best Practices for Quality Assurance
To mitigate challenges and maintain high standards in precision die cutting, implement the following best practices:
- Conduct Regular Inspections: Frequent quality checks during the production process can help catch errors before they become systemic.
- Maintain Equipment: Establish maintenance schedules for machinery to ensure optimal performance and extend the lifespan of critical tools.
- Utilize Controls: Implement statistical process controls to monitor variations and ensure consistency across production runs.
- Provide Design Feedback: Make collaborative adjustments with designers to refine specifications before production starts.
Performance Metrics for Die Cutting Success
Measuring success in precision die cutting requires the tracking of various performance metrics, such as:
- Yield Rates: Track the number of usable parts produced from each batch versus wastage to determine efficiency.
- Production Lead Times: Measure the time taken from order to delivery to gauge responsiveness.
- Defect Rates: Monitor the quality of the die-cut parts by keeping a record of any defects or inconsistencies found.
- Cost per Unit: Calculate the total production costs divided by the output to understand economic viability.
Future Trends in Precision Die Cutting
Technological Advancements Impacting Die Cutting
The future of precision die cutting looks bright with emerging technologies reshaping the industry. Innovations include:
- Automation: The advent of automation in manufacturing processes is set to increase efficiency, with machines capable of operating with minimal human intervention.
- Smart Manufacturing: IoT-enabled devices can help in real-time monitoring and analytics, enhancing productivity and reducing downtime.
- Sustainable Practices: More manufacturers are exploring eco-friendly materials and processes, reducing waste and energy consumption.
- Advanced Software: CAD and CAM technologies allow engineers to create more intricate designs and optimize cutting paths for efficiency.
Sustainability in Die Cutting Practices
As environmental concerns grow, sustainability is becoming a key consideration in precision die cutting. Businesses are adopting practices to minimize waste and enhance the recycling of materials, including:
- Material Selection: Opting for sustainably sourced materials and recyclable substrates can lessen the environmental footprint.
- Waste Reduction Techniques: Employing design strategies that maximize material usage and minimize scrap during the cutting process.
- Energy Efficiency: Investing in energy-efficient machinery and practices can help reduce operational costs and environmental impact.
Forecasting Industry Changes and Innovations
As industries evolve, so will the methods and technologies used in precision die cutting. Keeping abreast of market trends, such as shifts towards customization and personalization, will be essential for manufacturers looking to maintain a competitive edge. Additionally, the potential influx of new materials and processing methods may open new avenues for applications, making ongoing research and development critical for growth and innovation in this space.
Leave a Reply