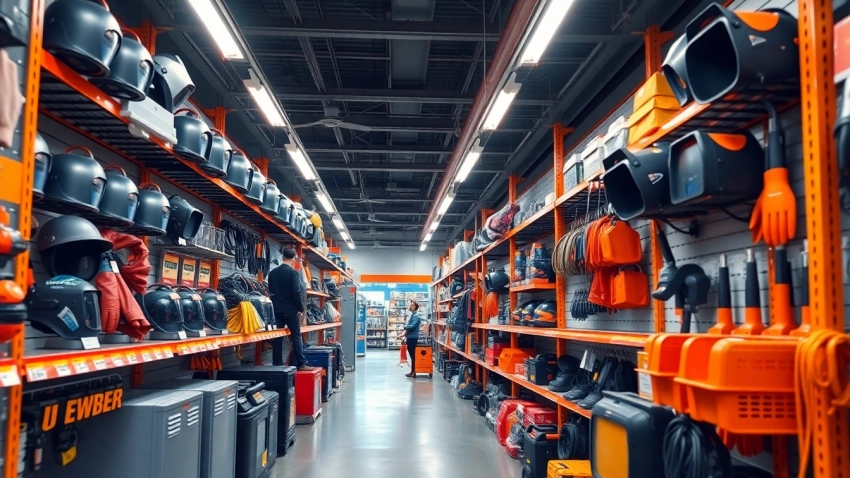
The Essential Guide to Buying Welding Supplies for Every Project
Understanding Different Types of Welding Supplies
Welding is an essential process in various industries, from construction to manufacturing, requiring precise equipment and quality materials. To achieve superior results, a welder must have access to a wide range of welding supplies. This guide delves into the different types of welding supplies, covering essential equipment, accessories, and significant brand comparisons.
Exploring Essential Welding Equipment
When considering essential welding equipment, it’s crucial to understand the basic tools and machines that every welder should have in their arsenal. Below are some pivotal components that play an essential role in the welding process:
- Welders: This includes MIG (Metal Inert Gas), TIG (Tungsten Inert Gas), Stick, and Multi-process welders. Each type is used for different welding tasks, from automotive repairs to heavy fabrication.
- Welding Helmets: These protect the welder’s eyes and face from bright light and sparks. Auto-darkening helmets are highly recommended as they adjust to the brightness of the welding arc automatically.
- Welding Gloves: A suitable pair of gloves protects against heat and electrical hazards. Look for gloves made of heat-resistant materials that allow for dexterity while providing adequate protection.
- Welding Wire and Filler Rods: These materials are vital for the welding process. Different types of wire and rods correspond to the welding process and materials being joined.
- Welding Tables: A sturdy, flat surface is essential for holding the workpiece securely during the welding process.
Choosing Quality Welding Accessories
Accessories may not be the main focus when setting up a welding shop, but they significantly impact the overall quality of the work. Here are some essential accessories to consider:
- Welding Magnets: Used to hold workpieces in place during the welding process, these magnets come in various shapes and sizes to accommodate different angles and configurations.
- Chipping Hammer: This tool helps remove slag from welds after the welding process, ensuring a clean finish and allowing for better inspection.
- Wire Brushes: Utilizing either brass, stainless steel, or nylon bristles, these brushes clean surfaces before welding and remove slag post-weld.
- Oxy-Acetylene Equipment: For those who do gas welding, this set includes tanks, hoses, and torches essential for cutting and joining metals.
Brand Comparisons in Welding Supplies
When it comes to welding supplies, numerous brands dominate the market, each offering unique advantages. Here’s a look at several popular welding brands:
- Miller Electric: Known for their durable and reliable products, Miller welders are favored in both automotive and construction industries.
- Lincoln Electric: This brand is often associated with advanced technology and a wide range of products, including consumables and welding machines.
- ESAB: Renowned for its innovation, ESAB provides high-quality welding equipment and is popular among professional welders.
- Harbor Freight: While primarily retailing budget-friendly supplies, Harbor Freight offers a variety of tools suitable for hobbyists or beginners.
Top Factors to Consider When Purchasing Welding Supplies
Making informed decisions when purchasing welding supplies ensures project success. Consider the following factors:
Assessing Your Project Requirements
Each welding project comes with unique demands. Analyzing specific requirements before acquiring equipment or materials is crucial. Key considerations include:
- Type of materials being used (steel, aluminum, etc.).
- Welding processes required for the project.
- The thickness of materials to be welded.
- Working environment considerations, including ventilation and safety risks.
Evaluating Safety Standards and Equipment
Safety cannot be overlooked in the welding process. Compliance with safety standards protects both the welder and the workplace. Ensure that:
- The equipment meets OSHA regulations.
- Proper personal protective equipment (PPE) is available and used consistently.
- There is adequate training for all personnel operating welding equipment.
Cost vs. Quality: Making Informed Decisions
While it may be tempting to choose cheaper options, investing in high-quality welding supplies often pays off in the long run. Poor-quality equipment can lead to:
- Increased safety risks.
- Less efficient welding processes.
- Higher costs due to repairs and replacements.
Conduct thorough research and read product reviews before making purchases to ensure quality without overspending.
Best Places to Buy Welding Supplies
Availability and accessibility of welding supplies vary depending on location and demand. Below are some buying options:
Comparing Online vs. In-Store Options
Purchasing welding supplies online offers broad choices and the convenience of home delivery. However, buying in-store allows buyers to physically assess tools and materials. Both options have advantages:
- Online Retailers: Sites like Cyberweld and WeldingSupply.com provide extensive inventories and often better prices.
- Local Stores: Physical stores provide the opportunity to consult knowledgeable staff and see items firsthand.
Local Suppliers and Their Advantages
Engaging with local suppliers often results in personalized service, which includes:
- Expert advice tailored to specific projects.
- Immediate access to supplies without long wait times associated with shipping.
- Opportunities for local discounts or loyalty programs.
Discounts and Wholesale Opportunities
Many suppliers provide discounts for bulk purchases. Businesses or frequent welders can benefit from:
- Wholesale shopping programs, offering reduced prices for larger orders.
- Seasonal sales or clearance events that help in saving costs.
Be sure to inquire about membership programs or discounts offered to professionals in the welding industry.
Maintenance Tips for Your Welding Supplies
Proper maintenance extends the life of your welding equipment and ensures consistent performance. Here are essential maintenance tips:
Proper Cleaning Techniques
Cleaning your welding equipment after each use removes contaminants that can affect performance. Employ the following methods:
- Use a wire brush to remove slag and contaminants on the welding torch.
- Regularly clean lenses on welding helmets to provide clear visibility.
- Wipe down machine components to prevent dust buildup.
Storage Solutions for Longevity
Effective storage can prevent damage and corrosion. Consider these tips:
- Store welding equipment in a dry, well-ventilated area.
- Use protective covers for welding machines and tools.
- Organize consumables in clearly labeled bins to avoid confusion.
Identifying When to Replace Equipment
Knowing when to replace welding supplies can save you from costly accidents or time delays. Signs of wear include:
- Rust or corrosion on metal parts.
- Diminished performance or erratic power output from welders.
- Visible damage to PPE, such as holes in gloves or helmets.
Regularly inspect your welding supplies and replace items as needed to maintain safety and efficiency.
FAQs About Welding Supplies
To further assist new and seasoned welders alike, here are frequently asked questions regarding welding supplies:
What You Need for Different Welding Projects
Different projects require specific tools and materials. Here’s a broad list of essentials:
- Welding helmet and gloves for safety.
- Type-specific welder for the job (e.g., MIG, TIG, or Stick).
- Consumables such as filler rods or welding wire.
Common Mistakes When Buying Welding Equipment
Here are some common mistakes to avoid:
- Not researching the specific needs of your projects.
- Overlooking the importance of safety equipment.
- Focusing solely on budget while compromising quality.
Understanding Welding Equipment Ratings
Familiarizing yourself with equipment ratings helps ensure you select the right supplies. Key metrics to consider include:
- Duty cycle, which indicates how long a welder can operate before needing a rest.
- Input power requirements, ensuring compatibility with available electric sources.
- Voltage settings, crucial for various materials and thicknesses.
Leave a Reply